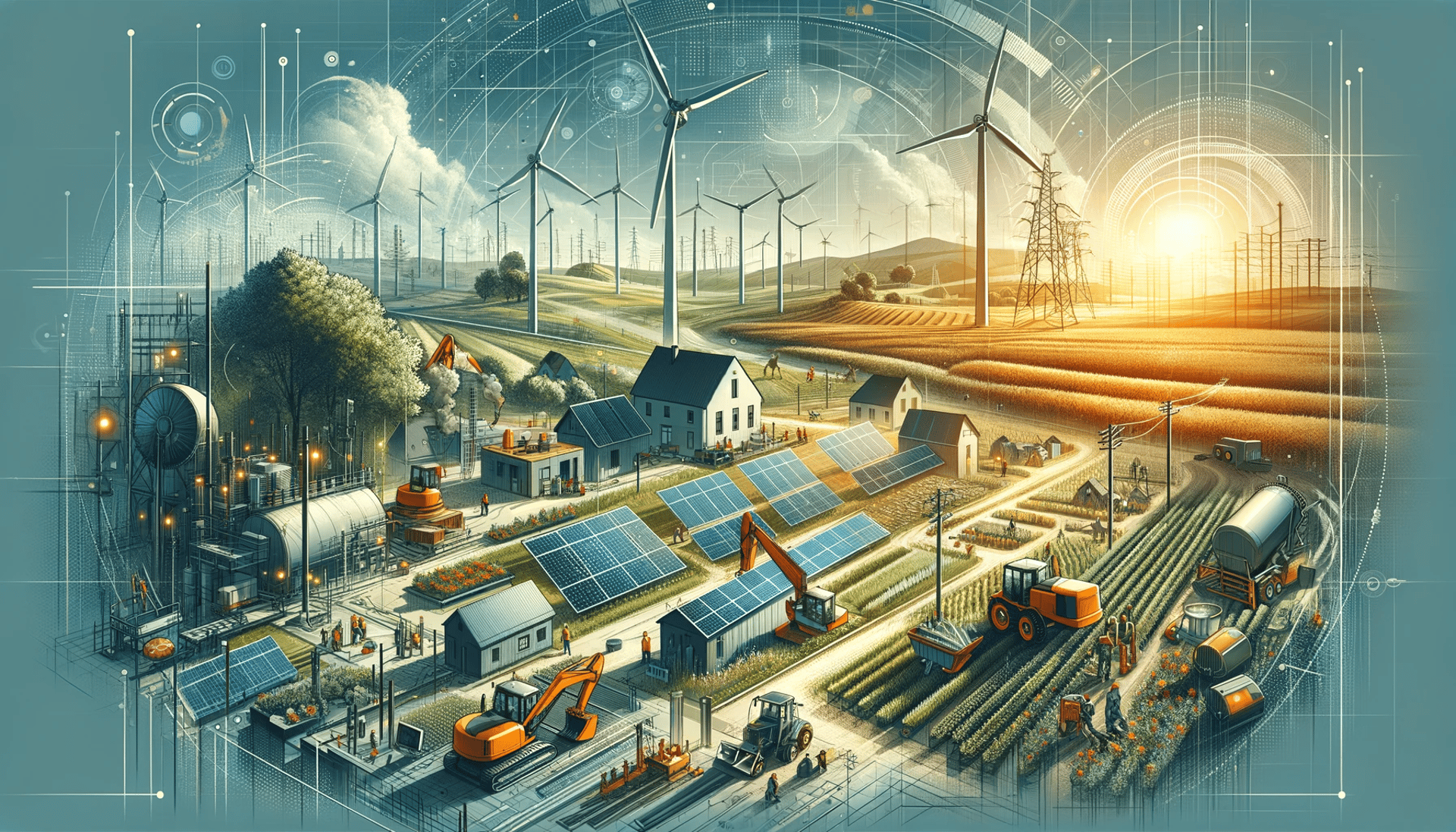
Building Visions into Realities
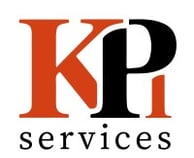
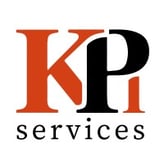
Our Story
At KPI Services, our mission is to strengthen and support the growth of industrial, commercial and agricultural businesses in the Fraser Valley through efficient and responsible construction management services.
As the proud owner and operator of KPI Services, Kim Percy brings a personal touch to construction management consulting. With over 50 years of experience in the industry, Kim's journey has included roles at all levels of construction, from direct fieldwork to executive management, including Chief Operations Officer and CEO of businesses with over 400 personnel and similar sized fleets of machinery.
A resident of Chilliwack for the past 30 years, Kim founded KPI Services in 2020 with the goal of helping other business owners avoid the unnecessary costs, delays, and risks of self-managed construction projects. Since then, KPI, has had the privilege to work with leaders of some of Chilliwack's most recognizable businesses.
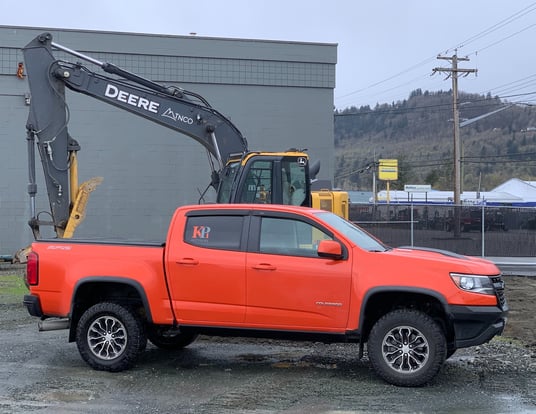
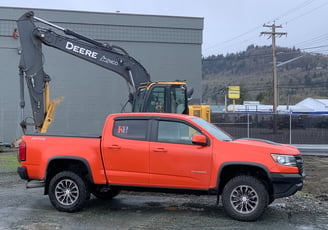
Dedicated to efficient, safe, and sustainable construction, realizing visionary projects

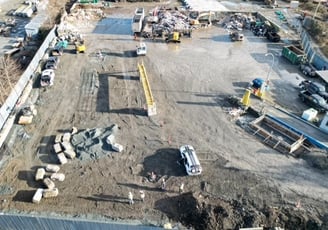
We offer project management, workforce safety programs, and sustainable construction practices focused on the specific needs of local businesses in the Fraser Valley.
By working closely with land-owners, local governments, and environmental agencies, we ensure our customers' visions are built efficiently, safely, and responsibly.
Our Projects
EZE Rent-it, Aldergrove (2021)
This 700 m2 site was an existing equipment rental yard and had been utilized since the 70’s, with little or no drainage or surface maintenance. The site had many areas where the asphalt was broken or missing as a result of increased load limits over the years.
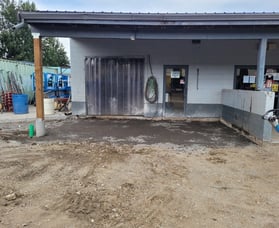
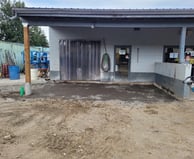
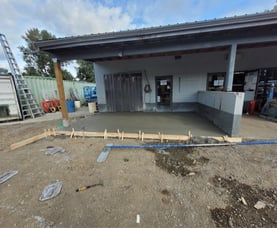
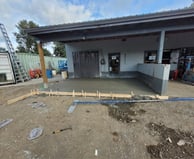
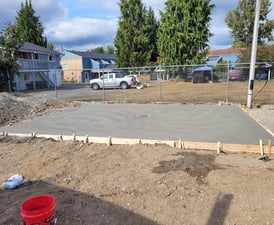
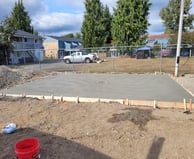
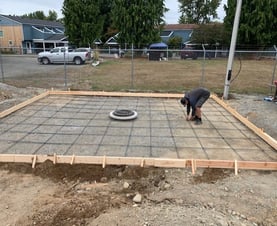
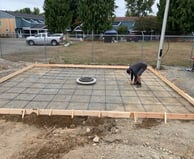
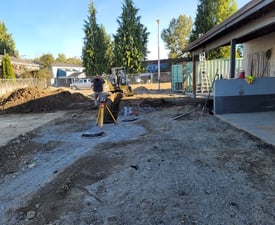
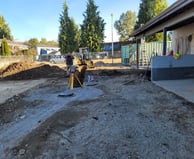
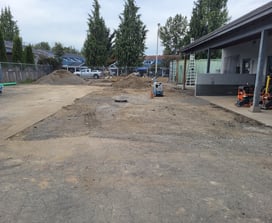
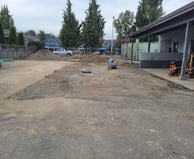
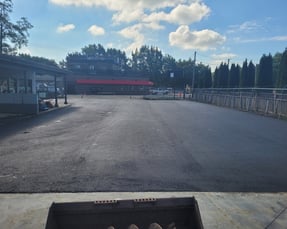
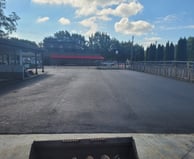

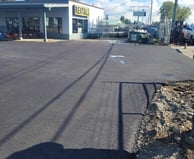
Design and Construction considerations and features
Abandoning and relocating the two previous wash down areas.
The installation of a 100m2 reinforced concrete slab with inverted crown
The wash pit debris flows into a proper catch basin with adequate sump to provide initial settlement prior to flowing into a new oil/silt separator
All other yard drainage also flowed into the o/s separator prior to connecting to the existing connection to the city storm system
Removal of existing asphalt and all soft or suspect areas were excavated
Proper sub-base and base aggregates were then installed and compacted to industry standards.
Aggregates were sufficient to handle the loads of the rental equipment and the stresses applied to the asphalt surface during loading, unloading and storage sequences.
Installed 3’ of a coarse graded asphalt, designed to handle the loads applied during the normal operation of the equipment rental yard.
All work was completed while maintaining safe and efficient daily operation of the business.
O’Connor RV Service and Maintenance Storage Yard (2022)
In 2022, O’Connor Collision changed operation to become their new RV Maintenance and Repair Facility. The gravel yard that had previously been used as a towing and recovery compound needed to be upgraded to better suit the storage of a variety of Recreational Vehicles prior to entering the Maintenance and Repair Facility.
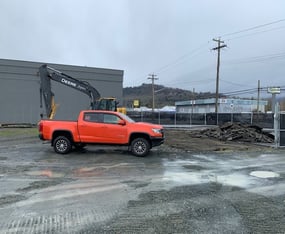
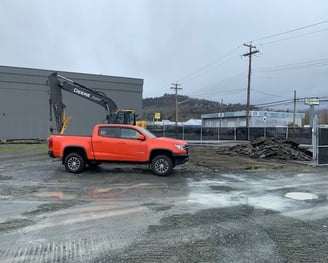
Design and Construction considerations and features
Existing aggregate material was tested and deemed to be suitable as sub-base aggregate.
Design elevations were adjusted to avoid hauling away materials to an expensive disposal site.
Consideration was also given to possible future use of the site for all final elevations and drainage design. Temporary use of lock blocks as well as permanent concrete wall for ultimate elevation requirements.
Design and install of a storm water management system, including retention and soak-a-way requirements in compliance with all City and Environmental concerns.
Application of 3’ of asphalt designed for the loads and stresses of the large vehicles.
New Sani Dump Station as well as new yard lighting and security system.
New concrete frontage sidewalk in commercial load entranceway.
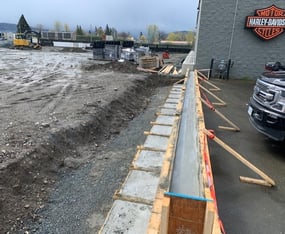
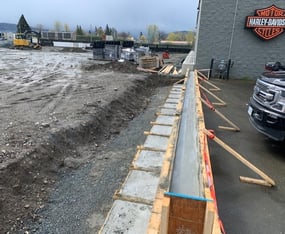
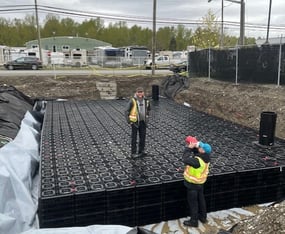
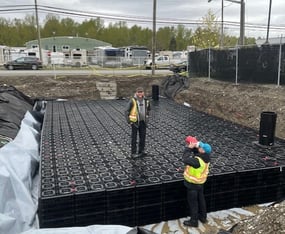
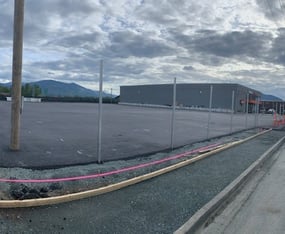
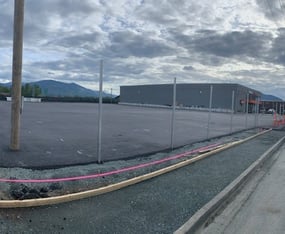
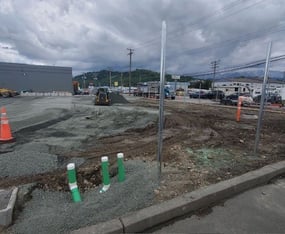
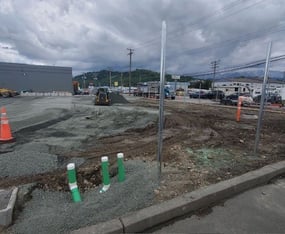
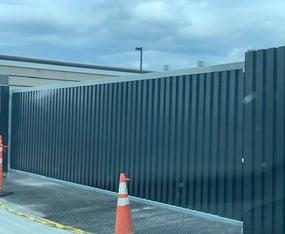
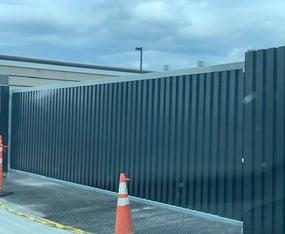
Valley Waste and Recycling Transfer Yard (2022 - 2023)
Valley Waste and Recycling Transfer Yard operate in a 3.5 acre site on Aitchelitz First Nation lands since 2008. They have always had continual environmental monitoring performed on the site and surrounding waterways and wanted to be more proactive in the stewardship of the lands they operate on. With that as a catalyst, John Verschuur approached KPI to act as the agent and Project Management to bring his vision to reality.
John imagined a solution that would eliminate the possibility of any contaminants from his operation, being able to enter the surrounding soils or waterways. He also sought a more efficient application to the processing and handling of the product from when it entered his location, until it was hauled away to an approved site.
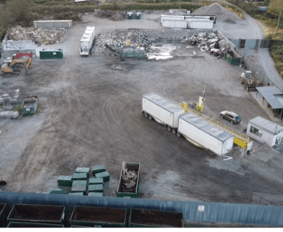
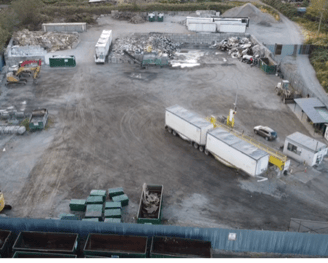
Design and Construction considerations and features
A plan was determined for relocating materials on-site to allow for a more efficient product handling flow.
All aggregate materials on site were tested and found to be free of any harmful contaminants
Existing aggregate material was tested for consistency and deemed to be suitable as sub-base aggregate.
Final elevations were determined so that only non-structural soils had to be removed from sight. Those organic soils were relocated to nearby fill sites.
Entire site has perimeter grading higher than the operating area, and a professionally engineered Storm Water management system incorporated, so that all surface water was treated prior to entering the oversized soak-a-way system.
A 17,000 ft2 covered structure was designed to provide a weatherproof sorting and handling area for the raw product. The loading of the processed product also takes place under the covered structure, virtually eliminating additional moisture being added to the material being loaded into the containers destined for landfills.
Addition of a new truck scale for out bound trucks, leaving the existing scale for inbound vehicles and thereby eliminating standing times and greatly reducing exhaust emissions.
The fully paved yard removes previous dusty conditions during the dry season and the messy mud puddles during the wet seasons.
All work was completed while maintaining safe and efficient daily operation of the business.
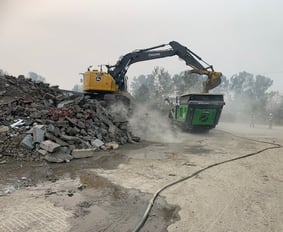
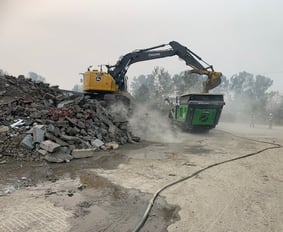
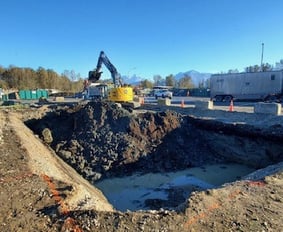
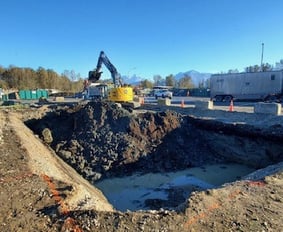
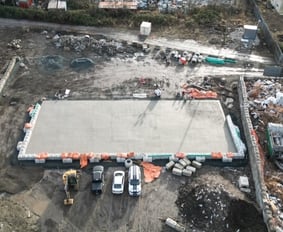
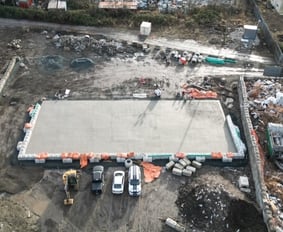
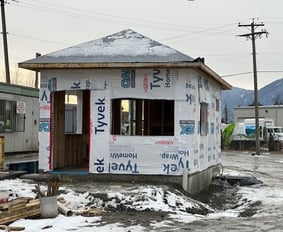
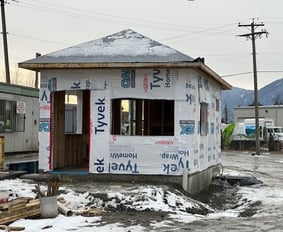
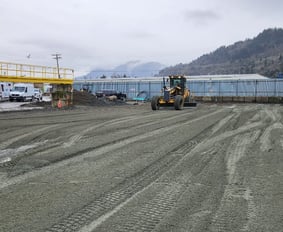
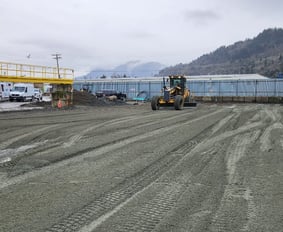
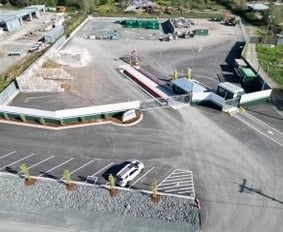
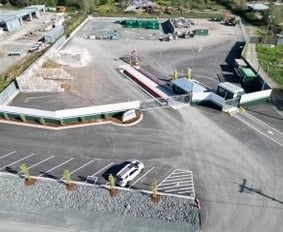
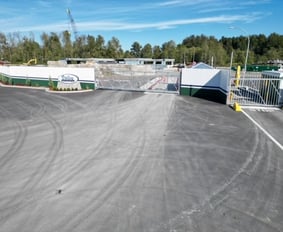
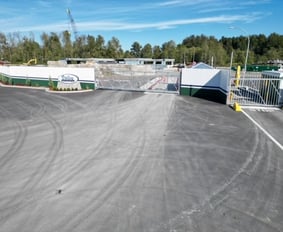
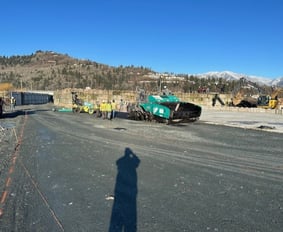
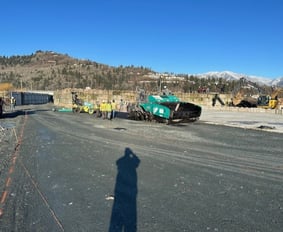
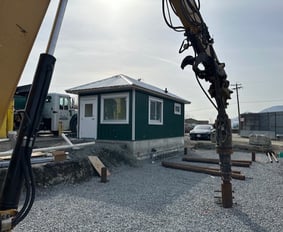
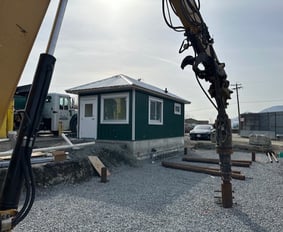
Contact Us
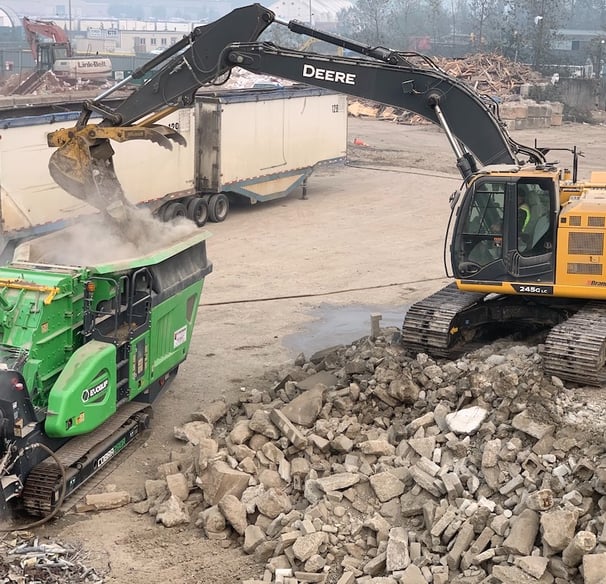
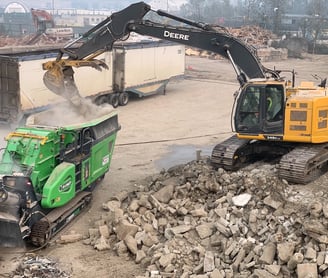